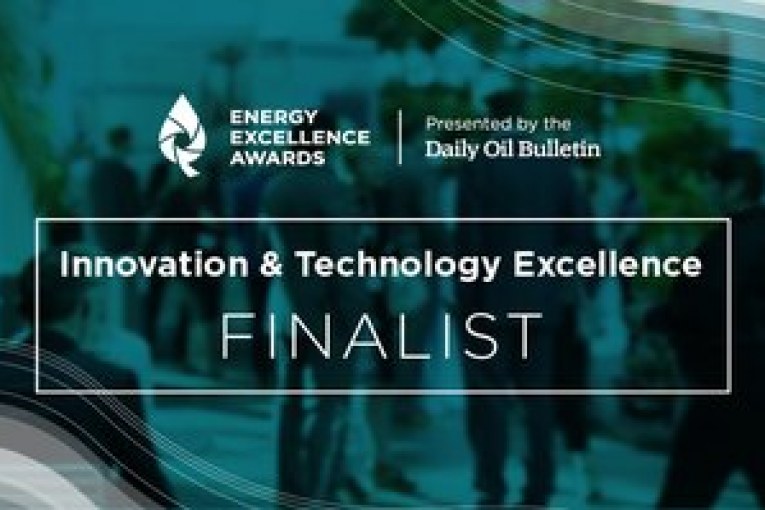
The second annual Energy Excellence Awards (EEAs) program, presented by the Daily Oil Bulletin, uniquely recognizes energy excellence and focuses on the advancement of collaboration within Canada’s energy industry.
The country’s oil and gas industry is entering what could be the most challenging period it has ever experienced. While the current COVID-19 crisis will undoubtedly touch each one of this year’s nominees, there may be no better time to celebrate the achievements of those developing the energy solutions for the future.
For 2020, the DOB received close to 90 nominations in four broad awards categories — Project Execution Excellence; Innovation & Technology Excellence; Exporting Excellence; and Environmental Excellence — recognizing work completed last year. The nominees were further broken down into 12 subcategories across the four groupings, before being judged by a committee of industry leaders.
From April 21 to May 6, we will be sharing the finalists in each of these subcategories. Today, we feature the best in Innovation and Technology Excellence in the subcategory of Production.
Special Note:Starting May 7, we’ll be hosting a series of special online webinar presentations to honour these companies and announce the champions in each category. Register here for these events.
With the oil and gas industry heading into an unexpectedly extended lower-for-longer price environment, brought on by a virtual worldwide lockdown due to efforts to control the coronavirus, controlling costs have become a matter of survival for many producers.
Fortunately, many will benefit from solutions developed early on in the downturn that has challenged the industry since the oil price crash of 2014. Those tough years have inspired many technology providers to go back to the drawing board to produce new ways of doing more with less.
Ambyinthas leveraged advanced artificial intelligence to adapt plunger lift systems to the new horizontal well environment. General Energy Recovery Inc. (GERI) has turned to an entirely new process to make steam production cleaner and more efficient, opening the door to smaller producers to tackle heavy oil recovery. And GHGSat Inc. has taken to outer space with new technology that drastically cuts the costs of emissions monitoring at a time when trimming emissions has become a necessity for all companies to succeed in the years ahead.
General Energy Recovery Inc.: Steaming ahead
The production of heavy oil typically requires significant up-front capital investment in large, permanent central facilities. They can involve a five- to 10-year planning horizon in order to optimize steam plant and production, with additional time and effort invested to secure regulatory approvals that include land disturbance and water supply issues.
As a result, projects typically require a significant oil pool size of greater than 50 million barrels of original oil in place to be economic, and many of the smaller fields are never developed. As well, currently used technologies do a generally poor job of extracting heavy crude from the reservoir — upwards of 90 per cent is left in the ground by cold heavy oil production with sand (CHOPS) wells in Saskatchewan.
GERI’s technology aims to change all that. The privately funded technology company, with operations based out of Lloydminster and head office in Calgary, leveraged its heavy oil expertise to develop a high-pressure portable direct contact steam generator (DCSG) that not only bolsters production, but reduces greenhouse gas emissions and water use.
The DCSG provides steam and flue gases for enhanced heavy oil production. Its current design has the capability of steam, CO2, nitrogen and heat output equivalent up to 75 cubic metres per day at 80 per cent steam quality.
Compact and mobile, requiring only a supply of natural gas and boiler grade water, the DCSG can be easily installed on existing wellsites with no additional land disturbance and quickly demobilized once steaming is completed.
The units are capital efficient at less than 10 per cent of the cost of once-through steam generation (OTSG) units commonly used by the industry, said GERI. And they eliminate the need for a central processing facility and steam pipelines, which lead to large energy losses along the way.
In field trials conducted in Saskatchewan on its own and in a nearby well with Canadian Natural Resources Limited (CNRL), GERI’s DCSG completed the largest steam/flue gas volume ever injected into a non-thermal well, the company said. The field testing was able to demonstrate a steam-oil ratio of only 0.58.
To date more than 18,000 bbls of incremental oil production has been realized. CNRL also noticed an increase in production from surrounding offset wells, according to GERI.
In addition, GERI was able to confirm at least 70 per cent of the CO2 was sequestered, and its DCSG produces 50 per cent less emissions and uses less water as 92 per cent of the steam/effluent energy is directed into the reservoir.
GERI also collaborated with the Saskatchewan Research Council’s (SRC) Post-CHOPs Well Test Centre to help validate DCSG performance. SRC’s multi-well CHOPS model integrated with Computer Modelling Group Ltd.’s STARS simulator was used to forecast expected reservoir response by history matching the oil, water and sand production data for the selected test well and several surrounding wells.
SRC’s field unit provided onsite gas analysis to confirm the volume of flue gas injected and sequestered in the reservoir. SRC’s direct involvement in the field trial also provided important third party validation of the results.
“The overall field trial provided the opportunity and results to determine performance, both technically and economically, including reservoir response of the GERI DCSG on post-CHOPS wells and its applicability for further application,” said GERI.
Completing field testing and demonstrating to industry with third party validation gave GERI the credibility for other producers to work with it to evaluate the potential for their operations, providing a new low-cost alternative to increase production with existing assets that meets their low-emissions goals.
GERI said it believes it can extend the application of its DCSG to steam non-thermally cased and cemented wellbores using its patented annular cooling loop technology. It is currently examining the potential for SAGD as well as tight, light oil applications in partnership with interested producers.
GHGSat Inc.: Sky’s the limit
Several countries — including Canada, the U.S. and Mexico in a deal signed in 2016 — have pledged to dramatically reduce methane emissions from oil and gas industry sources — in Canada’s case by 40-45 per cent by 2025. The challenge is, there is uncertainty about how much is being emitted, and around the clock monitoring to determine where it is leaking — and fix it — can be costly.
Several new technologies are under development to solve that challenge. Among the most advanced and potentially effective is a high-resolution satellite system created by Montreal-based GHGSat that can detect and quantify greenhouse gas emissions from selected industrial sites, anywhere in the world.
Among the first of a growing number of government and commercially owned satellite-based monitoring systems, GHGSat’s early stage solution has gained international attention after spotting previously unreported methane leaks at sites around the world.
The company’s spotting of a major leak in Central Asia equivalent to the fumes of a million cars reported last year was called “a major breakthrough” in the monitoring of pollution by news outlets after GHGSat reported the giant plume apparently emanating from a western Turkmenistan oil and gas field.
GHGSat was actually searching for emissions from naturally occurring mud volcanoes when it discovered the leak, a first for satellite monitoring. After notifying government authorities the release was stopped.
The company, which has taken several thousands of scans of methane leaks, also determined in 2019 that extinguished flares were responsible for the largest volumes of methane release. Gusts of wind and equipment breakdown cause flares to blow out, resulting in the discharge of methane that would otherwise be burned off to release less impactful CO2.
Greenhouse gas monitoring tends to rely on a patchwork of different technologies with varying degrees of accuracy. GHGSat’s patented, proprietary multi-platform system can provide consistency around the world in order to better measure, control and ultimately reduce emissions of GHGs, according to Stephane Germain, founder and chief executive officer.
“Using the same measurement technique, from orbit, for any site in the world provides a fair, transparent, precise and low-cost data-set that enables industrial operators to better manage their own emission and helps regulators measure the effectiveness of policies, resulting in reduced emissions worldwide,” he said in a company submission. “By using a satellite, we can rise above the different terrestrial methods of detection to get a bird’s-eye view of every site on the planet, no matter how isolated or remote.”
GHGSat makes use of a new generation of miniature satellites, about the size of a microwave oven, which are much cheaper to launch into orbit than conventional satellites. The company, which has opened an office in Calgary and grown to about 50 employees, plans to have a constellation of about a dozen satellites in orbit in the next three years.
In addition to GHG monitoring, GHGSat will ultimately also monitor for a range of air quality and other trace gases from anthropogenic and natural sources. Services are delivered using unique algorithms ingesting both GHGSat and third-party data to generate operational, environmental, health and safety, and regulatory insights, as well as market and government intelligence.
The company launched and demonstrated its first satellite called GHGSat-D, or “Claire,” in 2016. It met or exceeded most company objectives, demonstrating that measurements could be performed with 100 times higher spatial resolution than NASA and other national space agency satellites provide, in order to measure greenhouse gas emissions from individual facilities.
It also demonstrated that level of performance from a satellite that cost 100 times less than a typical NASA or other national space agency satellite, the company said, and showed that these measurements could be taken repeatedly, anywhere in the world, from many types of industrial facilities.
In shale plays, GHGSat’s solution can reduce costs to the operator by over 20 per cent while offering three times more measurements per year. By identifying large methane leaks through frequent monitoring, GHGSat said it enables operators to repair these leaks three to four times more rapidly, resulting in greater productivity from the repaired facilities.
In the oilsands, where existing methods to measure fugitive emissions are expensive, have significant uncertainties and require on-site measurements, GHGSat estimates its solution can reduce costs to the operator by more than 50 per cent while offering 12 times more measurements per year.
GHGSat worked with Canada’s Oil Sands Innovation Alliance (COSIA) in 2016-2017 to evaluate the use of satellite technology to measure GHG emissions from tailings ponds and mine faces. Measurements performed using Claire were inconclusive because of unrelated performance issues and the COSIA project was therefore extended for two years to enable additional measurements with GHGSat’s new satellite, GHGSat-C1, which was scheduled for launch in March. The COVID-19 crisis forced postponement of the launch to later in the year.
Among investors in GHGSat are the Oil and Gas Climate Initiative, Schlumberger Ltd., and the Business Development Bank of Canada.
Ambyint: Going horizontal
The shale gas and tight oil revolution that changed the history of the petroleum industry in many ways, including reviving the industry across North America, was ultimately a revolution based on technology. Horizontal drilling and multistage fracturing liberated vast quantities of oil and gas previously considered unreachable.
But the revolution also impacted on long used methods and technologies in the oilpatch, making them less effective. For example, in terms of artificial lift systems like the plunger systems that had become a preferred option for operators due to their reliability, operators have traditionally relied on Turner-Coleman and Foss & Gaul as the mathematical gold standard for optimizing plunger wells.
In use since the 1960s, these optimization equations work well for vertical wells. But they fall short for optimizing the newer horizontal wells that have become standard as horizontal drilling creates unique challenges, such as crooked wellbores, plungers set at 40 degrees deviation and slug flow from the horizontal legs.
Plunger wells thus experience sub-optimal production, diminished visibility into downhole conditions and generally excessive costs, notes Ambyint, a leader in artificial intelligence (AI)-powered production and artificial lift optimization.
Production optimization efforts for plunger wells are further hampered by manual data gathering across production accounting systems, SCADA and spreadsheets. In fact, most optimization processes are highly manual, which causes well issues to fall through the cracks, the company noted.
“Manual efforts explain why 80 per cent of plunger wells today have anomalies that could impact production. In a world where there are more wells than people to manage them, incumbent analytics, processes and optimization technologies simply do not bridge the gap for achieving on-plan and peak production — two important goals for operators focused on margin and higher free cash flow improvement,” said Ambyint.
At the highest level, optimizing plunger wells is a two-step process. First, operators must recognize and remediate production anomalies as they occur. Anomalies include well loading, surface restrictions, stuck plungers, leaking valves and miss-calibrated sensors.
Ambyint uses AI to identify anomalies faster and more accurately than current methods today. Once anomalies are evaluated and remediated, Ambyint’s improved physics models are a first step to determine optimal setpoints.
“Our updated models account for the unique physics of horizontal wells, providing more accurate representations of critical flow rate, critical lift pressure and plunger fall speed, which give engineers a better understanding of well conditions as well as an analysis framework that scales across an entire field.”
Once improved physics have been applied, artificial intelligence models are deployed to enable closed loop automation of setpoints. The AI model constantly evaluates well conditions to find the optimal configuration of setpoints, which maximizes production for each well at every point in time.
Ambyint, which maintains offices in Calgary and Houston, commercialized its plunger production optimization product in September. One of its first customers was instrumental in supplying initial well data that informed its anomaly detection and plunger optimization models, the company said.
AI-driven production optimization has significant business impact to an oil and gas producer, potentially increasing production up to seven per cent, reducing operating expenses up to 20 per cent and reducing failure rate up to 50 per cent, Ambyint said. “All three metrics have bottom line impact for operators and explain the strategic prioritization operators have placed on deploying production optimization technology.”
Ambyint utilizes more than 250 million operating hours to train and improve its optimization models and maintains the largest operating dataset of any company in the industry. Its physics-based approach coupled with subject matter expertise and artificial intelligence allows it to consistently generate value to operators with paybacks averaging two to three months.
The Innovation and Technology Excellence awards category is brought to you by our Industry partner, Fluor Canada.
Since 1949, Fluor Canada has been involved in the engineering, procurement and construction of a wide range of energy related projects that are spread across the Canadian landscape. Throughout its 70-year history in Canada, Fluor has provided local, regional and international clients with full-service capabilities, which include economic evaluations, conceptual engineering, feasibility studies, program management, detailed engineering, procurement, transportation and logistics, modularization, fabrication, direct-hire construction, construction management, commissioning, start-up, operations and maintenance.
You can read more of the news on source