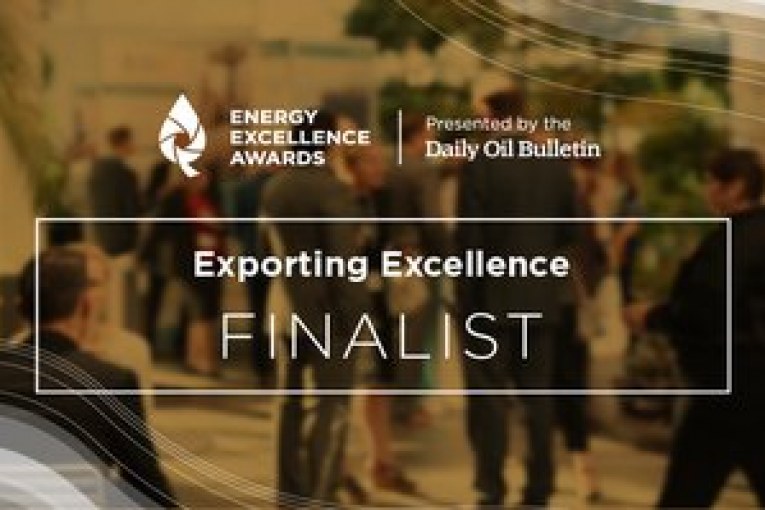
The second annual Energy Excellence Awards (EEAs) program, presented by the Daily Oil Bulletin, uniquely recognizes energy excellence and focuses on the advancement of collaboration within Canada’s energy industry.
The country’s oil and gas industry is entering what could be the most challenging period it has ever experienced. While the current COVID-19 crisis will undoubtedly touch each one of this year’s nominees, there may be no better time to celebrate the achievements of those developing the energy solutions for the future.
For 2020, the DOB received close to 90 nominations in four broad awards categories — Project Execution Excellence; Innovation & Technology Excellence; Exporting Excellence; and Environmental Excellence — recognizing work completed last year. The nominees were further broken down into 12 subcategories across the four groupings, before being judged by a committee of industry leaders.
From April 21 to May 6, we will be sharing the finalists in each of these subcategories. Today, we feature the best in Exporting Excellence in the subcategory of Advanced Technologies.
Special Note: Starting May 7, we’ll be hosting a series of special online webinar presentations to honour these companies and announce the champions in each category. Register here for these events.
As the oil and gas industry endures another bout of lower for longer prices amid an unexpected pandemic and resulting collapse in demand for its products, it will need to turn to technology to reduce costs like never before.
As with previous downturns, cost cutting has bred the winners that survive to thrive in the eventual upturn that resuscitates the industry. And invariably the cost cutting is derived from new technology, wherever it can be found. It is one silver lining for those companies that have developed cutting-edge new technologies that can give a leg up to those that adopt it.
Canadian companies leading in the Exporting Excellence in Advanced Technologies category can boast of technology solutions across the board, from reducing exploration risk to maximizing fracking efficiency to optimizing production through the life of a well.
Startup Interface Fluidics has improved downhole chemical performance screening with a microfluidic chip technology that takes the process from months to hours to complete. The so-called lab-on-a-chip technique has cut in half the costs associated with processes like coreflooding to determine aspects like permeability and interactions between the fluids and the rock.
Ambyintturned its attention to the evolution of horizontal drilling, which made some vertical drilling processes ineffective. It brought digital technology to bear on the optimization of plunger wells with new models that account for the differences encountered with horizontal wells, resulting in improved production and reduced operating expenses and failure rates.
And RS Energy Group turned to advanced data analysis to transform the company to a leading software-as-a-service technology firm sought out by majors for the incisive and actionable insights it can provide.
RS Energy Group: All-in transition to a digital platform
In creating its RS Prism platform, RS Energy Group (RSEG) leveraged the latest in intelligent digital technology to radically speed up data analysis and reporting, altering the way companies look at their data and make decisions.
RS Prism represents the industry’s first multidisciplinary, advanced analytics software platform that seamlessly integrates contextual insights, prescriptive and predictive analytics and advanced machine learning/artificial intelligence models to empower organizations and their technical teams to make rapid, more accurate decisions, the company said.
“Technology is the lifeblood of our business. Not only has it been a strong focus for the company since 2015, but it has transformed RSEG from a research shop into a true SaaS [software as a service] technology firm,” said the company.
Founded in 1998, RSEG has grown its international ambitions to the coverage of more than 150 companies operating in every key North American and many international energy plays. By 2015, RSEG had already begun to strengthen its team of engineers, economists, physicists, geologists, developers, financial analysts and mathematicians — all with a knack for forensic-style research.
The transition gathered speed after RSEG was purchased by New York-based private equity firm Warburg Pincus in 2015 in a deal worth approximately US$120 million, according to data compiled by Bloomberg. The value created by the transition is exemplified by the purchase of RSEG by Genstar Capital earlier this year in a deal that Bloomberg said values the Calgary-based energy research group — which itself had made at least two other acquisitions — at about US$1 billion.
Genstar is merging RSEG with another of its portfolio companies, Austin, Texas-based Enverus, previously known as Drillinginfo. Together the two companies employ 1,500 worldwide.
The genesis for developing RS Prism came from a need within RSEG itself, the company said. Its growing 110-plus person analyst team was writing deep, comprehensive research and intel on the oil and gas industry and just like its clients, spending weeks and months gathering and normalizing data sets before they could even start developing a meaningful thesis. The time and resource strain became more and more significant as the volume of data available in the public realm also increased.
RSEG hired a chief technical officer — an unusual hire in the energy market — to help transform the way it did business. After a year of evaluating various technologies, the CTO identified a powerful Silicon Valley techstack upon which RSEG began pouring its previously collected and curated data and analytics into — some 20 years of intel.
When RS Prism was conceptualized, the RSEG data science team worked closely with its expert analyst team to ensure the platform was user-friendly, fast and most importantly scalable so that it could house the top-tier analytics and models of today — and of tomorrow — in a single SaaS solution, the company said. “RSEG spent years developing RS Prism. It was critical that the foundation was comprised of the best, clean data sets to avoid a ‘house of cards’ as RSEG later began coding complex models and algorithms progressively stacked onto the baseline data.”
Today, it takes a single click in RS Prism to open a world of cleansed data, forward-looking predictions, artificial intelligence models and transformational solutions. “Our petrophysical data allows us to look deeper into a basin’s geology and map typography; our proprietary algorithms fill in gaps of missing production and completion data, in seconds; our predictive models help forecast the optimal well planning and development, before the operator even purchases acreage. All of this is done by the latest technology, constantly digitally reformed and reinvented,” added RSEG.
“As the technology was released to RSEG analysts, the speed and volume of information that it was capable of processing immediately revolutionized the process by which analysts wrote research, the time it now took to respond to client questions, and the deeper level of analysis we could do in one-tenth of the time. Transforming the workload for technical teams and engineers from 60-80 per cent data collection to renewed, high-value analysis and bottom-line, impactful decision-making has saved ourselves — and RSEG clients — millions of dollars.”
In 2015, RSEG had a small staff that was 100 per cent dedicated to writing highly technical, robust research. In the years since, its technology initiative to build the industry’s first single-solution, multi-disciplinary solution transformed it from 37 people to 350-plus today, with two-thirds of the employees focused on data science and technology.
Ambyint: Accounting for unique physics of horizontal wells
The shale gas and tight oil revolution that changed the history of the petroleum industry, liberating vast quantities of oil and gas previously considered unreachable, also impacted on long used methods and technologies in the oilpatch, in some cases making them less effective.
For example, the plunger lift systems that had become a preferred option for operators due to their reliability work well for vertical wells. But the optimization equations they rely on fall short for optimizing the newer horizontal wells that have become the hallmark, along with hydraulic fracturing, of the shale revolution. Horizontal drilling creates unique challenges, such as crooked wellbores, plungers set at 40 degrees deviation and slug flow from the horizontal legs.
Plunger wells thus experience sub-optimal production, diminished visibility into downhole conditions and generally excessive costs, notes Ambyint, a leader in artificial intelligence (AI)-powered production and artificial lift optimization.
Production optimization efforts for plunger wells are further hampered by manual data gathering across production accounting systems, SCADA and spreadsheets. In fact, most optimization processes are highly manual, which causes well issues to fall through the cracks, the company said.
“Manual efforts explain why 80 per cent of plunger wells today have anomalies that could impact production. In a world where there are more wells than people to manage them, incumbent analytics, processes and optimization technologies simply do not bridge the gap for achieving on-plan and peak production — two important goals for operators focused on margin and higher free cash flow improvement,” said Ambyint.
At the highest level, optimizing plunger wells is a two-step process. First, operators must recognize and remediate production anomalies as they occur. Anomalies include well loading, surface restrictions, stuck plungers, leaking valves and miss-calibrated sensors.
Ambyint uses AI to identify anomalies faster and more accurately than current methods today. Once anomalies are evaluated and remediated, Ambyint’s improved physics models are a first step to determine optimal set points.
“Our updated models account for the unique physics of horizontal wells, providing more accurate representations of critical flow rate, critical lift pressure and plunger fall speed, which give engineers a better understanding of well conditions as well as an analysis framework that scales across an entire field.”
Once improved physics have been applied, artificial intelligence models are deployed to enable closed loop automation of set points. The AI model constantly evaluates well conditions to find the optimal configuration of set points, which maximizes production for each well at every point in time.
Ambyint, which maintains offices in Calgary and Houston, commercialized its plunger production optimization product in September. One of its first customers was instrumental in supplying initial well data that informed its anomaly detection and plunger optimization models.
Ambyint is a technology partner with Amazon Web Services (AWS) and uses AWS Lamda and EMR to scale automatically and securely compute resources and data storage.
AI-driven production optimization has significant business impact to an oil and gas producer, potentially increasing production up to seven per cent, reducing operating expenses up to 20 per cent and reducing failure rate up to 50 per cent, Ambyint said. “All three metrics have bottom line impact for operators and explain the strategic prioritization operators have placed on deploying production optimization technology.”
Ambyint uses more than 250 million operating hours to train and improve its optimization models and maintains the largest operating dataset of any company in the industry. Its physics-based approach coupled with subject matter expertise and artificial intelligence allows it to consistently generate value to operators with paybacks averaging two to three months.
Interface Fluidics: Creating a reservoir analogue on a chip
In even the most effectively produced oil reservoirs large volumes of hydrocarbons are left behind, partly because producers just don’t have a good understanding of what goes on downhole. For example, how does the reservoir rock react with the chemicals pumped downhole, and how do the mix of chemicals react with each other in a given rock formation. The resulting inability to access greater volumes of hydrocarbons in a reservoir is a big problem, believes Interface, which has developed technology to help companies see what is truly happening.
“The industry is urgently looking for technologies that can increase the recovery rate and, in most cases, companies are being told to do more with less,” said the company, which is headquartered in Calgary and maintains a laboratory in Edmonton.
“There is a sea of chemicals available to operators that claim they will boost the recovery rate in a well,” Interface said. The problem is, there has been no way to validate these claims, and chemicals that work in one well could be damaging in another.
Interface has developed a test to identify the most effective fluid additives, and quantify their relative performance and compatibility with other fluids. The Interface Flowback Test assesses flowback fluid performance and compatibilities for its clients’ individual well as a successful chemistry will allow for the highest percentage of oil flowed back.
Interface creates physical analogues — silicon and glass analogues are modified to be representative of the reservoir material — with precision to sub-50 nanometre (nm, one-billionth of a metre) pore size that are representative of a client’s well.
“The test is run at the clients’ reservoir temperature, pressure and fluid flow rates, and the performance is measured both optically and using sensor data. By using machine vision software, the platform allows for visualization of performance mechanisms during the entire test run, unheard of in industry,” the company said.
Producers can quickly screen through several fluid additives, allowing them to make educated decisions as the testing is run under reservoir representative conditions, Interface said. The information provided by the flowback test helps clients make data-driven decisions on how to optimize field development, avoid potential reservoir damage and select optimal chemical vendors and products.
The test, which offers a repeatability unmatched in the market, provides relative results comparing chemistries to one another, providing clients with the data required to make strategic, cost-savings decisions that help them to recover more product per well.
“Operators are making chemical decisions based on our test results and analysis. There has been a high return rate of customers who have found value in the information and insight our technology provides — though this data is highly proprietary to them.”
Interface works with numerous operators and chemical companies in Canada, the United States, Norway, and the Middle East. It has worked, and continues to work, with the Alberta government, Economic Development and Trade in Norway, United Arab Emirates and the U.S. on various trade missions, accelerators and business development initiatives.
Norway state oil company Equinor formed a commercial partnership with Interface after it was selected as part of Equinor’s Techstars technology accelerator mentoring program. Interface is working with Equinor in both the offshore North Sea and shale plays in the U.S.
Interface’s Flowback Test technology has been the foundational piece of the company. “Operators, investors and partners in the industry truly believe in our technology,” Interface said. The company is continuing to commercialize new testing product lines internally in partnership with operators in North America and globally.
The Exporting Excellence awards category is brought to you by our Industry partner, Fluor Canada.
Since 1949, Fluor Canada has been involved in the engineering, procurement and construction of a wide range of energy related projects that are spread across the Canadian landscape. Throughout its 70-year history in Canada, Fluor has provided local, regional and international clients with full-service capabilities, which include economic evaluations, conceptual engineering, feasibility studies, program management, detailed engineering, procurement, transportation and logistics, modularization, fabrication, direct-hire construction, construction management, commissioning, start-up, operations and maintenance.
You can read more of the news on source