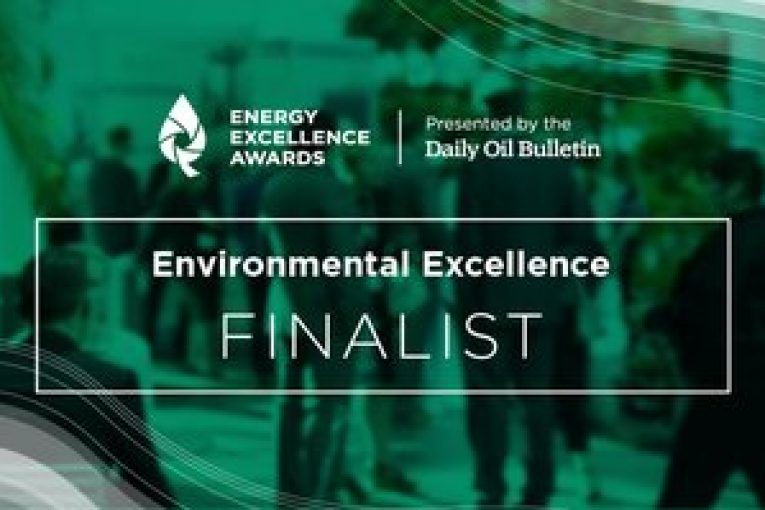
The second annual Energy Excellence Awards (EEAs) program, presented by the Daily Oil Bulletin, uniquely recognizes energy excellence and focuses on the advancement of collaboration within Canada’s energy industry.
The country’s oil and gas industry is entering what could be the most challenging period it has ever experienced. While the current COVID-19 crisis will undoubtedly touch each one of this year’s nominees, there may be no better time to celebrate the achievements of those developing the energy solutions for the future.
For 2020, the DOB received close to 90 nominations in four broad awards categories — Project Execution Excellence; Innovation & Technology Excellence; Exporting Excellence; and Environmental Excellence — recognizing work completed last year. The nominees were further broken down into 12 subcategories across the four groupings, before being judged by a committee of industry leaders.
From April 21 to May 6, we will be sharing the finalists in each of these subcategories. Today, we feature the best in Environmental Excellence in the subcategory of Cleantech: Air.
Special Note: Starting May 7, we’ll be hosting a series of special online webinar presentations to honour these companies and announce the champions in each category. Register here for these events.
Most industrial processes in Alberta, including conventional oil and gas and oilsands production as well as electricity generation, invariably create emissions associated with air pollution and climate change. As investors and consumers become increasingly concerned about climate change, it is becoming urgent that those industries decarbonize their processes to future proof for the decades ahead.
And so it is fitting that Energy Excellence Award finalists in the Cleantech: Air category have developed potentially groundbreaking solutions to solve the challenge in all of those areas.
In the oilsands, Canadian Natural Resources Limited’s innovative In-Pit Extraction Process could see a greenhouse gas emissions cut of up to 40 per cent. In conventional oil and gas, Westgen Technologies Inc.’s novel remote power generation and air compression package offers producers a cost-effective replacement for methane-emitting pneumatic systems at their wellsites.
And with an innovative new way to generate geothermal energy, borrowing heavily from oil and gas industry knowhow, Eavor Technologies Inc. is poised to fill the intermittency gap left by other clean energy sources such as wind and solar, providing zero air emissions heat and power around-the-clock.
Eavor Technologies Inc.: Leveraging oil tech for novel geothermal solution
The road to a low-carbon future has been made easier by the plummeting cost of renewables like wind and solar, but one major challenge remains — providing zero emissions power when the sun doesn’t shine and the wind doesn’t blow.
Calgary-based startup Eavor Technologies has leveraged oil and gas industry technologies to devise a potentially game-changing new way to access geothermal energy for scalable baseload power and heat. By making it accessible anywhere, anytime, the technology fills the intermittency gap left by conventional renewables.
The company’s Eavor-Loop geothermal power system is an industrial scale energy generation system that operates much like a massive subsurface radiator, collecting energy from the natural heat gradient of the Earth via a highly efficient and unique conductive system.
The closed-loop system comprises two vertical wells at either end connected via multiple horizontal multilateral wellbores, creating a closed buried-pipe system. A proprietary working fluid, sealed from the underground reservoir, is circulated through the loop to harvest heat, which can be used to generate electricity or in commercial heating/cooling applications. Because the working fluid is isolated from the environment, there is no risk of aquifer contamination and no need to access or treat water.
Unlike conventional geothermal power systems, Eavor-Loop does not require an existing underground reservoir of hot water, which eliminates exploration risk and makes it feasible anywhere, since the underground heat gradient is ubiquitous.
And unlike engineered geothermal power systems that fracture hot deep rock formations through which fluid is circulated, Eavor-Loop requires no fracking, eliminating the earthquake risk that hinders development of those emerging systems.
Its surface footprint is the lowest of any power source, it can operate completely independently and because it can be built anywhere, it can’t be held hostage to grid connectivity concerns, the company notes. Since it can provide dispatchable baseload power, Eavor-Loop does not require backup natural gas peaker plants, resulting in lower emissions than even wind and solar can typically provide.
Eavor constructed a demonstration project, Eavor-Lite, near Rocky Mountain House in central Alberta to both prove out all the innovative techniques and processes involved in an Eavor-Loop and to represent a geological proxy for the global market. Federal and provincial grant agencies contributed almost $9 million to the project, which was completed and third-party validated as having achieved all project objectives in December.
“Several learnings, processes and methods leading to new intellectual properties have come from the Eavor-Lite project,” the company said. “Now demonstrated at a commercial scale, Eavor-Loop holds the promise to transform the world’s energy stack, address climate change and provide socioeconomic balances: scalable, resilient, clean baseload power.”
By proving up the technology in Alberta, which is not advantageous to conventional geothermal power systems, Eavor showed that it could be done anywhere, said president and CEO John Redfern. “We arrived at a different solution than most people because we started with a different question. Most people ask, ‘how do I make geothermal better?’ And the answer is, go hotter and deeper,” he said.
“We didn’t have that option here. The sedimentary basin isn’t that deep…. So we were limited in temperature and that’s why we had to look for this more efficient solution. It is because Alberta [is so challenging] for geothermal that we came up with an innovative way of doing it.”
Eavor has many connections to the oil and gas industry. Shell New Energies functioned as both a supporting partner and observer to the demonstration project. Its in-kind contributions to the project, in the form of both project design and engineering support, served to de-risk many critical technical aspects of the project and Shell remains engaged with Eavor in its commercialization phase primarily in Europe.
Acting as vendor partner, Precision Drilling Corporation contributed both expertise and iron to help de-disk the project, Eavor said. Eavor-Lite presented an opportunity to use Precision’s High Performance, High Value services to drill the multilateral and connected horizontal wells, which was an important factor in achieving Eavor’s technical objectives.
Another Alberta company, Shear Fluids Ltd., worked closely with Eavor to design, source and implement specialty materials with relevance to its Rock-Pipe completions technology, critical to its unique and cost-efficient non-casing completions methods.
“Using Alberta energy services equipment, people and expertise, this project highlights the opportunity to put Alberta’s energy services sector back to work and repurpose a significant amount of the old, suspended and orphaned wellsites in the province,” Eavor said.
In January, Eavor entered into a partnership with Carmacks Development Corporation, wholly owned by the Little Salmon Carmacks First Nation, to deliver green baseload energy in the Yukon using Eavor-Loop technology. The company is also in advanced discussions for projects in other countries in Europe and Asia.
“The Eavor-Loop system has long been considered and theorized among geoscientist, engineers and generally within the energy industry, but had never been done before,” the company said. “Eavor’s technical innovations, now proven on a commercial level, have solved the technical issues holding back industrial-scale conductive heat harvesting so as to create the world’s first ever truly scalable form of green baseload power, the Holy Grail of power. That changes everything.”
Canadian Natural Resources Limited: Nimble mining approach cuts air emissions
GHG emissions are something of an Achilles’ heel for oilsands producers. While emissions have been declining on a per-bbl basis for decades, on average bitumen production remains an energy-intensive, and therefore above average emissions-intensive, process. With its innovative In-Pit Extraction Process (IPEP) — a relocatable, modular extraction plant that can be moved as the mine face advances — Canadian Natural Resources Limited (CNRL) hopes to change that.
Todays oilsands mining operations tend to be based on a megaproject type of infrastructure, involving the movement of vast amounts of material — from the overburden on top of the deposit to the ore itself — and then getting the ore from the mine to a central processing facility that is often kilometres away, explains Vince Wallwork, manager, Process Innovation.
There are also tailings materials, which in the existing process are fluid tailings, which are pipelined to dedicated disposal areas. “All that adds up to a lot of material movements and a lot of material movement adds up to a lot of energy,” he said.
Given cost pressures and environmental demands ahead — the company is looking to be carbon neutral at some future date — CNRL determined it had to do something different, he said. “Refining the existing process wasn’t going to get us to where we wanted to be. We really have to step-change.”
The IPEP process grew out of the concept of looking for a design to move material the least possible distance. The result was to build nimble: “It needs to be small, it needs to be relocatable so it can keep pace with the advance of the mine, and it had to create a dry, stackable type tailings material — so not something that was pumped, but something that was conveyable and could be backfilled into the mine. As we open pit we’ll be able to close pit and reclaim in a progressive fashion.”
By processing ore and separating bitumen right in the mine pit, IPEP’s modular extraction plant reduces materials transportation by truck, by pipeline length and by the energy needed to pump material. It also produces stackable dry tailings, eliminating tailings ponds.
The IPEP concept, currently being piloted at the company’s Horizon mine, could provide multiple wins for the business and the environment, according to CNRL.
In addition to significant GHG emissions reductions compared to conventional oilsands mining processing plants, it has the potential to reduce production costs by approximately $2 per bbl, while substantially reducing tailings management costs and liabilities.
It could also reduce the footprint of mining operations by eliminating the need for constructing new central ore processing facilities, and it could accelerate reclamation and reduce and avoid fugitive emissions through the production of dry stackable tailings.
The IPEP pilot is on track to meet all of its key performance indicators and CNRL said it is looking at making it commercial at 6,000 tonnes per hour production in the next three to four years.
The company has committed to making the technology available to oilsands mining companies through Canada’s Oil Sands Innovation Alliance for more rapid industry-wide adoption.
Westgen Technologies Inc.: Minding the methane emissions gap
Canada’s commitment to reduce methane emissions in the oil and gas industry by 40-45 per cent by 2025 has prompted several new technology initiatives as companies look to meet the target in as efficient and low-cost a way as possible. For Westgen Technologies, that lowest cost opportunity lies in eliminating pneumatic methane venting on wellsites.
Natural gas-driven pneumatic controllers and pumps are one of the leading sources of methane emissions from oil and gas operations, responsible for up to 35 per cent of methane emitted. New regulations will restrict the use of fuel gas pneumatic controllers in 2021 in British Columbia and 2022 in Alberta. Existing high bleed pneumatic controllers will need to be retrofitted or converted to instrument air one year later.
But there is a gap in power generation levels often needed at the wellsite to produce instrument air. Established technologies such as thermoelectric generators, fuel cells and Stirling engines generally only generate four kilowatts or less using fuel gas/wellhead gas. On the other end of the spectrum, technologies such as reciprocating internal combustion engines and microturbines can be used to generate 35 kilowatts and greater, at much higher cost.
“This gap in power generation, to deploy instrument air, is the root cause of our industry’s legacy of venting gas to atmosphere through pneumatic devices,” notes Westgen. It is the gap that Westgen technology aims to remedy.
The Calgary startup’s first product, called EPOD (engineered power on demand), supplies the necessary power for off power-grid wellsites to eliminate methane venting through pneumatic devices.
The EPOD is a hybrid design powered primarily by solar energy combined with an advanced battery system and a reciprocating gas engine (wellhead gas capable) to provide back up power. Designed to comply with new and emerging methane regulations, the EPOD is the most cost-effective technology to produce between five and 30 kilowatts of power using wellsite fuel gas, the company said.
For new wellsites EPOD can replace several traditional components such as power generation, motor control centre, solar battery hybrid pump power packages and glycol heat tracing heaters. “By combining common components into a modular shop fabricated package, EPOD reduces the overall capital cost of building a new wellsite compared to traditional designs,” said Westgen.
Reduced operating costs are realized through improved reliability, fewer maintenance callouts with remote monitoring and the ability to take the fuel gas to market and avoid carbon taxes. Westgen has also used the technology platform to expand to those remote applications requiring instrument air or power to run small industrial applications, the company added.
In a pilot with Painted Pony Energy Ltd., the EPOD was found to emit between nine and 15 tonnes CO2-equivalent per year for the typical six well pad, reducing wellsite emissions by 99.5 per cent. Westgen has since been working with two other companies to install EPODs on their sites.
Westgen collaborated with Bluesource, a global company in the environmental market space, to use their carbon credit expertise and provide validation for the carbon credits generated by EPOD installations.
Westgen has developed an innovative business model that can help oil and gas companies meet their emissions reduction objectives when there is very little extra capital available,” the company concluded. “Westgen offers the service of developing the carbon credits to producers in regions where carbon credits are available. Partnering with Bluesource, Westgen can offer EPODs to producers for little or no upfront capital so that they can finance their installation on the basis of carbon credits.”
The Environmental Excellence awards category is brought to you by our Industry partner, Fluor Canada.
Since 1949, Fluor Canada has been involved in the engineering, procurement and construction of a wide range of energy related projects that are spread across the Canadian landscape. Throughout its 70-year history in Canada, Fluor has provided local, regional and international clients with full-service capabilities, which include economic evaluations, conceptual engineering, feasibility studies, program management, detailed engineering, procurement, transportation and logistics, modularization, fabrication, direct-hire construction, construction management, commissioning, start-up, operations and maintenance.
You can read more of the news on source