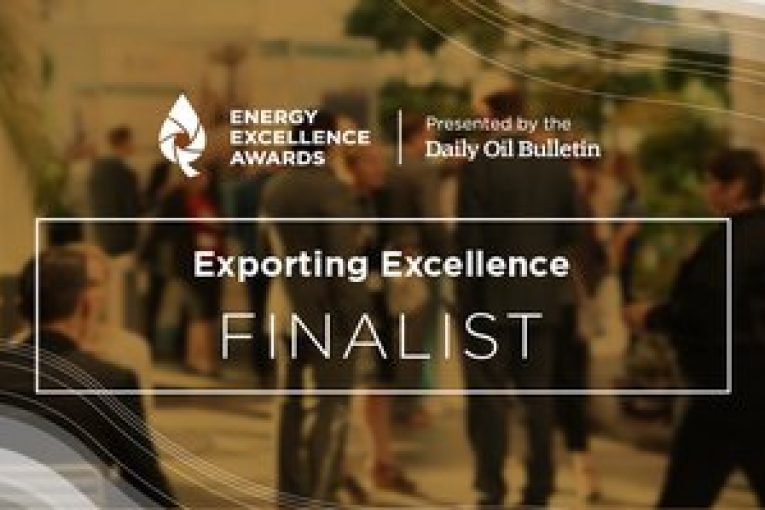
The second annual Energy Excellence Awards (EEAs) program, presented by the Daily Oil Bulletin, uniquely recognizes energy excellence and focuses on the advancement of collaboration within Canada’s energy industry.
The country’s oil and gas industry is entering what could be the most challenging period it has ever experienced. While the current COVID-19 crisis will undoubtedly touch each one of this year’s nominees, there may be no better time to celebrate the achievements of those developing the energy solutions for the future.
For 2020, the DOB received close to 90 nominations in four broad awards categories — Project Execution Excellence; Innovation & Technology Excellence; Exporting Excellence; and Environmental Excellence — recognizing work completed last year. The nominees were further broken down into 12 subcategories across the four groupings, before being judged by a committee of industry leaders.
From April 21 to May 6, we will be sharing the finalists in each of these subcategories. Today, we feature the best in Exporting Excellence in the subcategory of Cleantech.
Special Note: Starting May 7, we’ll be hosting a series of special online webinar presentations to honour these companies and announce the champions in each category. Register here for these events.
Recent studies have shown methane emissions from oil and gas industry facilities are higher than previously thought, prompting a worldwide crackdown on leaks and fugitive releases of the potent greenhouse gas. In Canada, regulations to track and repair methane leaks and to limit emissions from equipment like pneumatic devices have already gone into effect.
Increasingly, natural gas flaring has come under the spotlight as well as the fracking revolution has led to an upsurge in flares to burn off associated gas for which the infrastructure to take to market has not kept up. One recent study found that more than one in every 10 flares operating at oil and gas sites in the Permian Basin was either unlit— venting uncombusted methane straight to the atmosphere — or only partially burning the gas they were releasing.
Meeting mandated reductions targets is a challenge that has created opportunity for Canadian companies ahead of the curve in mitigating emissions with unique new and existing technologies that are simultaneously beneficial for the environment and for the bottom line.
Questor Technology Inc.has spent a quarter century perfecting its patented waste gas combustion technology, adding waste heat recovery opportunities to the mix to provide a much sought after solution in jurisdictions most rigorous in mandating emissions reductions.
Fellow Calgary-based company Valence Natural Gas Solutions has taken a different technology route to meet a similar objective — to eliminate unnecessary and inefficient flaring in a way that puts waste to use, by allowing producers to use the otherwise unexploited gas to power their operations.
Questor Technology Inc.: A technology whose time has come
In 2015, the leaders of Canada, the U.S. and Mexico signed on to a landmark methane emissions reduction target of 40-45 per cent from across the continent’s oil and gas industries by 2025. Other countries as well as oil majors have since announced their own emissions cutting targets for the critical short-lived climate pollutant, responsible for some 25 per cent of global heating.
Such efforts are good news for Questor Technology, a company with a unique technology package to efficiently incinerate methane at the wellhead while generating power. Questor secured a $5.8-million deal with Petróleos Mexicanos (Pemex) in 2019 to supply its clean combustion incineration and power generation technology at three oil and gas production facilities in Mexico.
Compared to flaring, a correctly operated incinerator can yield higher efficiencies through proper mixing, gas composition, retention time and combustion temperature. Questor’s high performance incineration system destroys in excess of 99.99 per cent of methane, volatile organic compounds and other hazardous pollutants. And its subsidiary, ClearPower Systems, uses organic rankine cycle (ORC) power generation systems to convert the system’s waste heat to power that can be used to run a wellsite, evaporate produced water or sell to the grid.
In Mexico, Questor technology installed at 13 sites previously venting associated gas — predominately methane with hydrogen sulphide gas (H2S) — will save the operator 450,000 tonnes of emissions per year for the next decade at a cost of less than $2 per tonne, well under the country’s carbon tax. Diesel power generation was eliminated.
“This technology saved power generation costs but most importantly it improved the quality of life for the people living in close proximity to the sites. Efficiently destroying the H2S eliminated odour and improved safety,” notes Questor.
The export deal was “another example that our effective and cost-saving solutions transcend borders,” commented Audrey Mascarenhas, Questor’s president and CEO.
In addition to commercializing its Waste Heat to Power technology in Mexico, in 2019 Questor also penetrated new markets in New Mexico, Texas and Pennsylvania while maintaining a strong presence in Colorado. Early in 2020 it also grew its business in the Permian in Texas and New Mexico, an area ripe for expansion as flaring has become a major issue for producers.
“Other encouraging signs [in 2019] included stricter state emission regulations with a focus on methane, our clients’ commitments to emission reduction targets, the general public’s expectations of clean energy and the enquiries initiated by the power generation projects in Mexico,” noted the company.
In fact, stricter emissions rules are driving much of Questor’s international expansion as the company fairs best where regulations are strongest. Over 90 per cent of the company’s incinerator rental fleet is located in Colorado, which mandates the use of enclosed combustion (incinerators) and now targets methane, and in North Dakota where regulation supports demand for Questor’s proprietary high efficiency waste gas incineration systems. “Colorado is ground zero for a combination of oil and gas production and environmental stewardship,” Mascarenhas stated in a release last year.
Questor is diversifying into other sectors that will further drive exports as it transitions from an oilpatch service provider to a clean-tech-focused emissions data firm. The company — whose technology solutions can be used in landfills, agriculture, biodigesters, manufacturing plants and other emission-producing industries — has already expanded into the Caribbean, Western Europe, Russia, Thailand, Indonesia and China. Its export success helped the company deliver its highest ever yearly revenue and earnings in 2019.
Still, tough times lie ahead as the coronavirus-inspired lockdown devastates the oil industry. In an April 22 statement addressing the crisis, the company said that during this time “we will be focusing on gaining market share, educating our customers around our solutions for combating emissions, diversifying out of oil and gas and expanding our waste heat to power offering into other industries and applications.”
Praising the federal government’s $750-million Emission Reduction Fund announced on April 17, with a focus on efforts to cut methane emissions, Questor also said it is “currently evaluating its opportunities to offer its products and services to support the initiatives and is excited to potentially play a role to showcase its abilities.”
Zeroing out emissions
To support the company’s transition, a corporate rebranding is underway. Among other things, Questor said it will continue to build its digital capability focused on an emissions platform. It is proceeding with its new emissions excellence centre in Calgary, known as GEMMA, which will offer predictive emission monitoring (PEMS), ensuring companies meet their regulatory emissions targets.
“We will continue to build our digital capability focused on an emissions platform that will eventually enable us to credibly quantify emission reductions for our clients and guarantee a zero emissions site, with the end goal of monetizing the emission reduction offsets,” said Questor.
“The resilient companies that survive these challenging times will continue to focus in the medium to long term on addressing the commitments they have made to their investors and the public, which includes reducing greenhouse gas emissions,” the 25-year-old company concludes. “Questor’s proven, cost-effective technology solutions will play an instrumental role in enabling these companies to meet their goals and targets. As these companies ramp up and return to normal activity levels, Questor will be ready.”
Valence Natural Gas Solutions: End-to-end flare gases capture solutions
Valence Natural Gas Solutions has designed in Canada and deployed in North Dakota an innovative flare gas capture and use technology. Through deployment of this unique technology, significant volumes of flaring have been abated and economic value has been captured for the customer, royalty owner and the state of North Dakota. Rather than being flared off, this gas is instead captured and re-deployed to the front end of the drilling and completions process.
By powering rigs and other equipment in the field off of gas that would have otherwise been flared, the environmental footprint of producers’ North Dakota operations have been dramatically reduced. Since the initial deployment for a major international producer, other operators have also adopted the technology.
The technology originated with the Ferus Group of Companies, from which Valence was spun out a few years ago. Initially Ferus, a full-service cryogenics business that supplies liquid nitrogen and CO2 to field operators, examined switching its vehicle fleet to run on natural gas. But it quickly determined that the bigger benefit lies in supplying natural gas to the wellhead.
Compressing and liquefying natural gas is similar to that of liquefying nitrogen and CO2, for which the Calgary and Houston headquartered company already had the expertise to produce.
“We basically said, ‘This isn’t just about fuelling our trucks, there is actually a business here to start going down the road of displacing diesel with natural gas,’” explains Valence president Stewart Wilson. “The on-road market is not the low hanging fruit. The best way to attack it is the high horsepower engine — the drilling rigs, the frac pumpers — at a lot of the same locations we’re going out to for nitrogen. There’s a pretty standard, cost-effective kit that you can bolt on to diesel engines to run them on natural gas.
“So we built out infrastructure to move natural gas around in liquid form and supply it for high horsepower engines, as a cleaner and cheaper fuel…. That was when the North Dakota Bakken [shale oil play] was just kind of getting into that full commercial production mode and the flaring was starting to become headline news.”
Massive volumes of associated gas were flared from the tight oil wells as gas pipeline construction could not keep up. “We had this big problem where there’s gas being flared, just down the road from the drilling rig, so [we asked] how do we connect the two? How could we go right out to the wellhead where it’s otherwise flaring, capture it, and move it just down the road to fuel customers in the field.”
Valence technology was the result. “We developed the technology to basically process the gas at the wellhead. Once you’ve cleaned up the gas, you plug it into a high pressure compressor, compress it into high pressure tubes, basically, that are on a truck, and then we drive that gas out to a drilling rig and run the rig off of it.”
Progressive iterations of the technology have dramatically improved its efficiency. “We’re really excited about where we’re at now,” said Wilson, noting the latest units are currently under construction in Calgary.
“What we’ve got essentially is an up to four million cubic foot per day, shallow cut gas plant completely on wheels. If there was a flaring problem, we can roll up, be set up in the matter of five or six days, start processing gas, compressing it, moving that gas away, and completely silencing the flare. We get it into the engine with the same customer, allowing the customer to basically use their own gas.”
After the associated gas is exhausted or can be put in a pipeline, “we pack up our plant [and] move it down to the next location and kind of keep following the flaring problem as it pops up through a basin — like whack-a-mole, we have a mobile solution to do that.”
While North Dakota, which has very high associated gas rates, is the perfect market for Valence, the company also operates in Saskatchewan and Alberta and, notwithstanding the current market collapse brought on by the coronavirus lockdown, plans to expand to Texas and other areas where flaring presents an ongoing challenge.
The Exporting Excellence awards category is brought to you by our Industry partner, Fluor Canada.
Since 1949, Fluor Canada has been involved in the engineering, procurement and construction of a wide range of energy related projects that are spread across the Canadian landscape. Throughout its 70-year history in Canada, Fluor has provided local, regional and international clients with full-service capabilities, which include economic evaluations, conceptual engineering, feasibility studies, program management, detailed engineering, procurement, transportation and logistics, modularization, fabrication, direct-hire construction, construction management, commissioning, start-up, operations and maintenance.
You can read more of the news on source