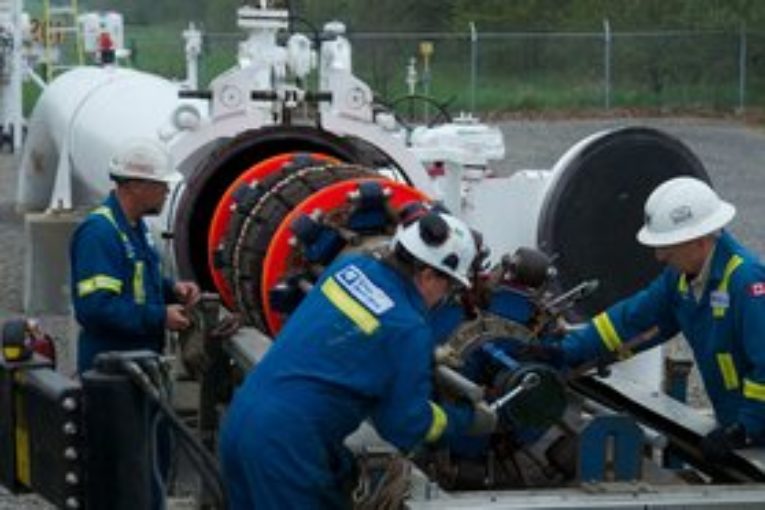
Pipelines have always been the safest option for transporting large volumes of oil and gas. As technology evolved over the years, so has safety, efficiency and environmental performance, impacting every dimension of the pipeline industry, from the metallurgy and quality control in the manufacture of pipe, to pipeline construction processes, maintenance, leak detection, monitoring and spill response.
At the front end, pipeline companies building new infrastructure today all vet their vendors carefully. These assessments ensure that pipe mills conform to the latest standards manufacturing. They look at control points, assurance steps and certifications. High levels of automation and quality control ensure consistency in the product that reaches the field.
“There’s also been a significant focus on quality in the construction of pipelines to enhance safety and performance,” says Vik Kohli, director engineering services, Enbridge. His engineering oversight for Enbridge’s liquid assets extends to process safety management. He is also chairman of the Canadian Energy Pipeline Association (CEPA) Foundation.
”These pipelines will be in the ground for decades, so the quality of the initial build is incredibly important,” Kohli says.
Automation is part of the construction process. Automated pipe welding and automated liquid applicators for coating pipe girth welds deliver more consistent results. Automated girth weld coatings improve safety for workers by minimizing exposure to harmful chemicals and result in fewer repairs than manual application.
“If we can reduce the number of those pinholes or misses or any of the rework that goes in the field, you’re going to see a higher longevity of the asset and less money to maintain it over time,” says Chelsey Reschke, general manager, Keymay Industries, which recently introduced an automated girth welding technology for smaller diameter pipelines.
“There’s a lot of focus on the big-diameter pipelines, but the distribution of incidents by diameter of pipeline indicates that the area where this innovation would be best applied is actually in the 10 to 20-inch pipeline market,” she says.
Many ideas for pipeline safety, such as cathodic protection in tandem with pipe coatings to protect against external corrosion, have been used since the early days of pipelining. Technology advances have simply made these concepts stronger.
“We now use fusion bond epoxy (FBE),” Kohli says. “This coating is, in essence, baked into the steel. It’s very high quality and everyone uses it now.”
Pipe coatings in the 1950s were tar enamels. These coatings were actually very effective, but they were also carcinogenic, and some mixtures included asbestos, so they weren’t safe for the environment or workers.
“In the 1960s and 70s, the industry started trialing some coatings that were good for the environment, but they weren’t very durable or effective,” Kohli says.
Advances in materials led to the adoption of fusion bond epoxy, which is inert to the environment and safe to handle. With automated girth coatings now matching the epoxy on the rest of the pipe, the result—in theory—is a pipe in the ground that has a continuous film of corrosion protection.
“There’s the issue of damage prevention as an external threat. We still have pipelines being hit by machinery or when digging, but a lot of good work has been done on that front as well,” Kohli says.
Cathodic protection—the use of low-voltage electric current to protect the pipe against oxidation—is another time-tested corrosion mitigation science. It hasn’t changed much over the years, but the most recent improvements in inline inspection (ILI) tools—or “smart pigs,” to use industry jargon—now allows pipeline operators to pinpoint weak points in the cathodic protection system.
ILI tools came into commercial use in the 1980s and 1990s. Moving through the inside of the pipe and scanning for potential problems in the steel pipe was a pivotal milestone in the evolution of pipeline safety and environmental performance.
“From an integrity standpoint, we’ve gone from external prevention, which was cathodic protection as the main source of mitigating the threat of corrosion, to basically a medical MRI of your pipeline,” Kohli says.
Initial ILI tools targeted metal loss, dents and geometry. As more competitors entered the market, the features these tools could see could be sized more accurately. The shift from analogue to digital formats saw a proliferation in the ILI technology and miniaturize in the 2000s.
“Combinational technologies became possible,” says Daryl Ronsky, vice president at Rosen Canada, a global leader in ILI technology. “Enhanced assessment techniques came out and ultrasonic crack detection started to become a possibility. Today, we’re able to monitor material properties in pipelines, we have very high-resolution technologies and big-data techniques are being applied to analyze that data.”
Modern ILI tools can identify a variety of defects in pipelines by combining five or six inspection device technologies onto one unit to tackle difficult to detects issues.
“Cracks are unique challenge,” Ronsky says. “Lots of different cracks can occur. There are hook cracks, lack-of-fusion defects, mechanical damage causing cracks, narrow external corrosion, gouges and dents, over trends, undercuts and, of course, the particular phenomenon we’re familiar with in Canada, stress-corrosion cracking.”
All of these are difficult to detect and discriminate, but the latest advances in electromagnetic acoustic transducer (EMAT) technology allows for a new level of detection and quantification of these small defects that can lead to pipeline spills, Ronskay says.
Pipeline companies help in the continuing evolution ILI accuracy by sharing its data with vendors. A pipeline company will dig up its pipeline for maintenance based on the features detected by ILI tools. This field work proves out whether the tool was right or not. By sharing that information with the tool vendor, its data sets continually improve.”
Another tool in the pipeline integrity toolkit is the use of inhibitors.
“Inhibitors are an injection of chemicals into the line at various points,” Kohli says. “An inhibitor eliminates water, if water is present. It reduces the oxygen if there’s any in the line—usually through water—so it helps prevents oxidization of the line from the inside.”
Technology advances have also improved the monitoring for leaks and the ability to respond to a spill. The introduction of mass balance systems (MBS) involves measuring the volume of product at intervals along the pipeline and making calculations to determine whether the mass of the product remains within predictable norms. Anomalies suggest losses due to leaks.
“Like ILI tools, mass balance systems have seen technology advancements to where now we are using ultrasonic metres,” Kohli says. “This led to significant improvements in the size of the leaks we can detect.”
Regulatory bodies, such as the Alberta Energy Regulator, typically require an integrated approach to leak detection. This includes direct visual assessments from patrolling pipeline rights-of-way for evidence of leakage or other issues, in-service pressure testing, mass-balance monitoring and instrument-based data collection.
Pipelines that were once managed by people communicating over phones and manually turning valves at pumping stations are, today, run from a centralized control centre. Enbridge’s control room, for example, is in Edmonton. It’s completely self-sufficient in its capacity to operate the company’s entire system throughout North America.
This level of centralization and oversight requires a lot of computing power. Higher levels of automation of certain control functions that eliminate the need for human intervention—for example, if a system becomes over-pressurized, automated release systems are activated—add to that computing load. The interpretation of data from the latest generation of ILI tools, running integrity maintenance and system optimization also demands significant computing power.
“We rely on massive computing centres that run analysis much quicker,” Kohli says. “There’s an effort to continue a trend towards removing human error from the equation by building more programming and allowing computers to assess what is going on and to take action based on our programming.”
The current digital transformation, which will include the development of artificial intelligence, is also expected to lead to further pipeline safety and environmental performance improvements over the next decade.
You can read more of the news on source